新能源新材料系列研究:复合集流体行业简析

泛海投资
来源:泛海投资
复合集流体是锂电池技术升级的重要方向之一,其中复合铝箔能够解决高能量密度场景下的安全性需求,复合铜箔能够显著降低成本、减轻电池重量。2023年是复合集流体的量产元年,百亿蛋糕亟待分切,业内企业百舸争流,布局正当时。
一、基础概念
(一)集流体
1、什么是集流体?
集流体是锂电池电芯中正负极的重要组成部分,作为汇集电流的结构或零件,其作用是承载正极和负极的活性物质,并将活性物质化学反应产生的电流汇集起来形成较大的电流进行对外输出,从而完成化学能向电能的转换过程。
锂电池工作原理示意图
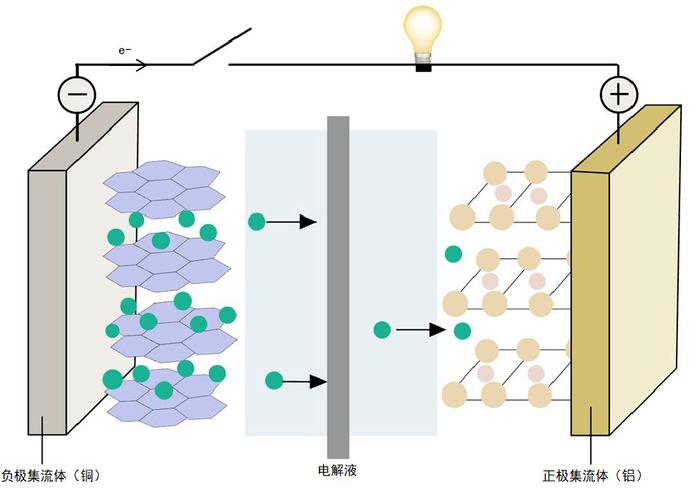
IAPS
2、集流体需具备哪些特性?
理想的集流体需要满足电导率高(利于电子传输从而提高锂电池比容量和倍率性能)、化学与电化学稳定性好(不与活性物质、粘结剂和电解液发生相互反应)、机械强度好(防止碰撞等外力作用下变形对电池造成的伤害)、具有较强的粘结强度(与电池活性物质兼容性和结合力好)、廉价易得(从而能够实现大规模的生产制造)等特性。
3、集流体的传统方案是什么?
目前,锂电池集流体通常负极采用铜箔,正极采用铝箔。铜在较高电位容易氧化,适合作为负极集流体;铝在充当负极集流体时腐蚀问题较严重,适合被用为正极集流体。
(二)复合集流体
1、什么是复合集流体?
复合集流体是新型的集流体材料,不同于传统集流体使用纯铝箔/纯铜箔,是以 PET/PP等高分子材料作为中间层基膜,通过磁控溅射/真空镀膜/水电镀等工艺,在基膜两侧镀铝/铜导电层所形成的复合材料,是一种类三明治的夹层结构。
复合集流体结构示意图
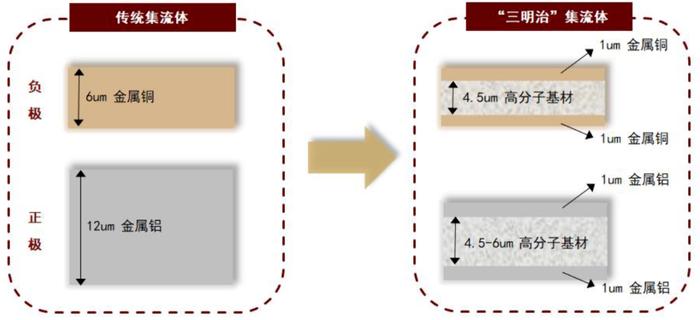
2、复合集流体具备哪些优势?
(1)复合铝箔能够解决高能量密度场景下的电池安全性问题
传统集流体材料受压易断裂,产生大尺寸毛刺后易刺穿隔膜,造成内短路从而引起热失控。而复合集流体由于导电层厚度较薄,产生的毛刺尺寸小,且中间高分子不易断裂,即使断裂也无法达到刺穿隔膜的强度标准,有效防止锂枝晶穿透隔膜引发的热失控。此外,高分子材料为绝缘材料,受热会发生断路效应,因此短时间内可大大降低短路电流,电池安全性能得到大幅提升。
(2)复合铜箔能够显著提高电池重量能量密度、降低电池成本
由于高分子基膜质量较轻,且金属导电层厚度变薄,复合集流体重量较传统集流体显著降低。以6μm厚度的复合铜箔为例,其中4μm的铜被4μm高分子材料替代,铜的密度8.96g/cm³,高分子材料的密度1.38g/cm³,粗略测算复合铜箔电池相较传统铜箔电池可减重约50%。随着集流体重量占比降低,电池内活性物质占比增加,重量能量密度可提升5%-10%。
原材料成本方面,传统铜箔为纯铜构成,而高分子材料替代部分铜,按照目前铜价6.3万元/吨,PET切片价格约为1万元/吨,PP切片价格约为0.8万元/吨,材料成本优势明显。制造成本方面,当前复合集流体尚未达到量产阶段,制造成本相较传统铜箔未具备明显优势。随着设备工艺不断优化,产品良率不断提高,叠加大规模量产后摊薄设备与厂房折旧成本,预计规模量产状态下,复合铜箔相较于传统铜箔约有20-30%成本优势。
(三)工艺路线
1、复合铝箔主要采用真空蒸镀工艺
复合铝箔主要采用真空蒸镀工艺,生产工序可分为真空反应镀膜-真空镀铝-分切/打包储存等。
首先是真空反应镀膜环节,通过在原膜上使用化学气相沉积的方法沉积5-15nm的铝的氧化层作为膜面的活化物质使得原膜活性化。其原理是在设备真空度<5×10-2Pa时通过蒸发舟作为铝的蒸发载体向高温蒸发舟上送入铝丝,以电加热的方式,在950-1000℃的温度条件下将固态铝气化,铝蒸汽沿着垂直热场方向向基材表面扩散,同时在铝蒸汽扩散的通道上方通入氧气,使得氧气能与铝充分发生反应并沉积在基膜表面,形成一层致密的抗蚀层。
其次进入真空镀铝环节,第一步是使用镀膜氧化铝的物料作为基膜,通过物理气相沉积的方法,在抗蚀层表面继续沉积金属铝,最后形成完整的沉积铝层。第二步是设备控制在真空度<2×10-2Pa,加热方式与第一步相同,均是通过电加热的形式使得温度上升到950-1000℃从而气化固态铝,由于气态铝平均自由程大于蒸发源和基体的距离,因此会沉积到基体表面,从而形成厚度为800-1000nm的导电铝膜,膜面导电性通常可达到40-30mΩ。整个镀膜过程均在真空条件下进行,且膜背面与通入-20℃至-30℃冷却液的棍体紧密接触,使得膜在发热时可以急速降温,因而分子得以凝结在膜表面,同时通过冷却液控温可以避免基膜达到热熔温度、发生形变。
2、复合铜箔采用的工艺包括磁控溅射、真空蒸镀、水电镀
目前业界使用的生产方法主要为两步法(真空磁控溅射+水电镀)和三步法(真空磁控溅射+真空蒸镀+水电镀)。区分两步法及三步法的核心步骤是真空蒸镀环节,真空蒸镀相对于磁控溅射而言铜沉积效率更高,由于第一步磁控溅射线速度较低(线速度越快,单位时间沉积的铜越少),铜膜沉积速率慢,加入真空蒸镀之后生产效率会大幅提升,但三步法的缺陷在于使用蒸镀设备时作业温度较高,而高分子材料在高温作用下可能受到热损失,这一难点在产业上仍需时间解决,因此目前主流还是使用两步法进行生产。
(1)真空磁控溅射
由于高分子材料的结晶度大、极性小、表面光滑等特性,会影响镀层与基材之间的黏合力,且高分子材料大多数为不导电的绝缘体,因此无法直接进行电镀,需要先对高分子材料进行表面处理、活化等,使其表面沉积一层导电的金属膜。
采用真空磁控溅射技术镀膜是制作复合铜箔的首个步骤,可分为真空磁控溅射活化及真空磁控溅射镀铜两个环节。
真空磁控溅射活化是采用高分子材料作为基膜,通过PVD的方法,控制设备本体进入真空状态,再通入纯净的氩气(一般纯度大于 99.99%),电子在真空条件下,在飞跃过程中与氩离子发生碰撞,使其电离出氩正离子和新的电子。受磁控溅射靶材背部电池的约束,大多数电子会被约束在磁场周围,氩离子在电场力的作用下加速飞向阴极靶,并以高能量袭击铜合金靶表面,使靶材发生溅射,在溅射粒子中,中性的靶原子或部分离子沉积在基膜上形成薄膜,厚度一般为5-20nm,导电性一般为1000-3000Ω。
真空磁控溅射镀铜是采用通过真空磁控溅射活化工艺的物料作为基膜,在真空磁控溅射设备中进行镀膜,原理及过程与真空磁控溅射活化相同,最终形成10-40nm的沉积薄膜,导电性一般为 10-20Ω。
磁控溅射是目前复合集流体的核心工艺之一,其优势在于低温升、高速率以及薄膜及衬底之间的结合力强,但实际操作过程中存在以下难点:1)收放卷及张力控制。高分子基膜比较薄,收放卷时容易起皱发形,控制材料不变形是工艺难点之一。2)生产效率。磁控溅射线速度较低(线速度越快,单位时间沉积的铜越少),铜膜沉积速率较慢。3)基膜容易受损。磁控溅射的过程需要高压放电,如果没有控制好磁/电场,可能出现粒子轰击损害基膜的情况。
(2)真空蒸镀
真空蒸镀环节是区分复合铜箔制造两步法与三步法的核心环节。真空蒸镀是指在真空条件下,利用加热蒸发的方式蒸发镀膜材料并使其气化,材料粒子逸出形成蒸气流,入射到基片表面,凝结形成固态薄膜的工艺方法。
真空蒸镀是不采用溶液或电解液制备薄膜的干式镀膜方法,具有成膜方法简单、操作容易、薄膜纯度和致密性高、膜厚均匀等优点。与磁控溅射相比,蒸镀法镀膜对铜的沉积效率更高,能够大大加快生产节拍。但真空蒸镀的缺点也很明显,加热蒸法的方式需要在高温环境下进行,容易造成高分子材料的损伤从而导致产出复合铜箔的良率降低。
(3)水电镀
目前主流的两步法是真空磁控溅射活化及镀膜之后跳过真空蒸镀,直接进入水电镀环节。在磁控溅射初步形成底层铜膜(30-70nm)后,铜基膜的膜面导电性已满足酸性离子置换条件,此时可通过水介质电镀增厚的方式将铜层增厚至1μm左右,实现集流体的导电需求。
水电镀指的是电解质溶液在外电流的作用下,在基材表面上镀上一种或几种金属 (非金属)过程。其原理为将基材膜面金属层浸在金属盐的溶液中作为阴极,无氧铜作为阳极,接直流电源后,在基材膜面金属层上沉积出所需的镀层。水电镀的技术相对成熟稳定,且因工艺简单,从设备到环境的要求均没有真空镀苛刻,被广泛应用。
3、高分子基膜选材
目前主流的高分子基膜选材主要为PET膜和PP膜:
PET(聚对苯二甲酸乙二醇酯)化学性质为耐弱酸弱碱,不耐水蒸气,高分子层表面附着力、材料耐高温性以及材料机械强度优于PP材料;目前基材耐酸碱性不影响生产工艺。
PP(聚丙烯)化学性质为耐强酸强碱,耐腐蚀性优于PET材料;具有很好的光学性能,透明度好;在高温下不释放有毒物质。但铜层在高分子层面的附着力较差,且PP熔点较低,溅射工艺中基膜易被击穿,导致良品率较低。
目前行业尚未形成标准化的复合铜箔技术指标参数,对于有机材料基膜的选择尚未明确。综合成本和性能要求,短期看PET基膜的工艺难度较低、进展最快,长期看PET/PP均有可能被选择,最终结果尚需下游电池厂家测试验证。
二、市场空间
复合铝箔主要应用于高镍三元电池等高性能密度电池场景,因电池能量密度越高,热失控和燃烧爆炸风险越大。复合铝箔目前制造成本较高,相比于传统铝箔(约1-2元/㎡)很难有价格优势,因此,复合铝箔应用场景较窄,仅有高能量密度且对成本不敏感的电池场景能够使用。
复合铜箔相比于纯铜箔具备减重和降本优势,复合铜箔有望替代传统铜箔广泛应用于动力和储能等场景,预估2023年为复合铜箔量产元年,假设2023-2026年复合铜箔渗透率由5%逐步爬升至40%,2026年对应复合铜箔需求为280亿㎡,复合铜箔市场规模超500亿元。
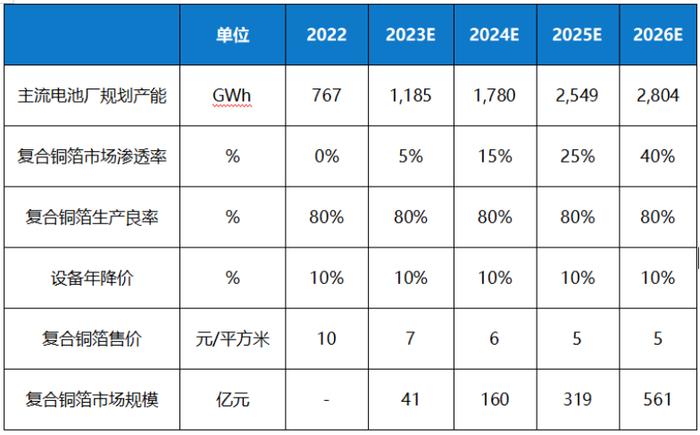
三、行业发展阶段
过去几年,复合铜箔已经走过了研发和技术突破阶段,即将进入规模量产阶段,目前复合铜箔产业化趋势明确,2023年将成为量产元年。
第一阶段:研发布局阶段(2017-2021):出于优化电池安全性的目的,电池厂对在集流体中加入有机夹层进行研究并设立研发专利。2017年宁德时代率先提出了使用PPTC作为金属集流体内部的夹层,形成“三明治”结构降低电池短路热失控风险。复合集流体逐渐在动力电池、消费电池等领域替代传统的电解铜箔、铝箔投入试用,进入产业高度关注阶段。
第二阶段:技术突破阶段(2022-2023H1):材料厂商以及电池厂商进行密集的技术验证,磁控溅射、电镀、超声焊等设备工艺持续迭代升级,当前国内多家膜材料厂商以及传统电解铜箔凭借工艺共通性积极布局复合箔材,且已与上游设备厂商签订批量订单,提前锁定优质产能。根据设备的交货节奏来看,复合铜箔的小批量产能有望于2023H1形成。
第三阶段:规模量产阶段(2023H2后):随着焊接工艺、产品良率等难点逐渐解决,复合铜箔产业化进程加快,预计2023Q3-Q4复合铜箔有望开启大规模量产,2024年复合铜箔动力电池有望在主流车型上实现搭载装车。
四、市场格局
复合集流体产业链上游为原材料和设备厂商,中游为复合集流体制造厂商,下游为动力、储能、消费电池厂。在复合集流体领域进行布局的公司包括上市公司和初创公司。上市公司包括宝明科技、万顺新材、元琛科技、方邦股份等。初创公司包括金美新材、安迈特等。
根据公开资料整理,各家发展情况如下:
(一)宝明科技
1、基本情况
宝明科技是一家专业从事LED/CCFL背光源及触摸屏研发、生产和销售的上市公司。宝明科技于2022年7月28日公告,布局锂电池复合铜箔领域,公司拟在江西赣州投资建设锂电池复合铜箔生产基地,主要生产锂电池复合铜箔。
2、建设及产能情况
宝明科技赣州复合集流体项目总计划投资60亿元人民币,一期拟投资11.5亿元人民币,二期拟投资48.5亿元人民币。根据2022年7月投资者关系活动记录表,一期项目2022年7月已签订投资合同,计划建设期为12个月,计划最晚2023年8月完成建设。预计一期将于2023年2季度量产,一期计划达产后年产能1.5-1.8亿平米锂电复合铜箔,相当于传统铜箔约一万吨,对应产能14-15GWh。根据2023年2月公告,宝明科技与安徽马鞍山市宁马新型功能区管委会签订投资建设合同,拟在马鞍山投资建设锂电复合铜箔生产基地,总投资62亿元,用地约360亩,分两期建设。
3、客户情况
根据2022年10月投资者关系活动表,宝明科技PET复合铜箔一期生产设备已开始陆续交付,已送样至多家电池企业进行验证。现阶段国内外主要客户大都处于测试验证阶段。
(二)万顺新材
1、基本情况
万顺新材是一家专注于环保包装材料的上市公司,业务包括功能性薄膜业务、铝加工业务、纸包装材料。万顺新材拥有进口电子束镀膜设备、磁控溅射设备、水电镀设备等多套核心设备,PET铜箔产品也正在有序研发阶段。
2、建设及产能情况
子公司江苏中基以包装铝箔为主,现有产能8.3万吨;安徽中基以电池铝箔为主,在建7.2万吨高精度电子铝箔生产项目中一期4万吨项目于2021年年底开始投产,二期3.2万吨项目计划明年开始投产,另外万顺新材于2022年非公开募集15.9亿元用于扩增10万吨动力及储能电池箔产能,正在安徽中基筹建年产10万吨动力及储能电池箔项目,项目全部建成后2024年将形成25.5万吨铝箔总产能。
3、市场拓展情况
万顺新材目前已成功开发出应用于电池负极的PET复合铜箔样品并送样。
(三)元琛科技
1、基本情况
元琛科技致力于环保领域烟尘治理,主要产品包括脱硝催化剂与除尘滤袋,应用于火电、钢铁、水泥等非电行业烟尘治理。元琛科技2020年开始布局复合集流体,2021年正式立项复合集流体。
2、建设及产能情况
元琛科技于2021年获得一块面积为130亩的化工用地,用于建设循环材料产业园,其中包含集流体项目。2022年12月第一条量产中试线已经完成了设备安装调试,正式开始产品生产,已完成首条复合铜箔产品生产线的达产工作。首批产品于近日顺利下线,下线产品性能经检测,各项指标均达到预期。
3、客户情况
计划2023年元旦左右送样至CR5厂商客户。
五、投资观点
我们认为,相较于传统铝箔,复合铝箔成本上没有显著优势,因此只适用于高能量密度电池场景,市场空间有限。而复合铜箔不仅能够降低成本,而且减重以提升电池能量密度,广泛适用于动力和储能领域,有望替代传统铜箔方案,未来市场广阔。我们看好在复合铜箔领域率先具备量产能力并占领市场先机的厂商。泛海投资持续关注新能源新材料领域,并已储备了多家复合集流体企业的投资机会。
举报成功