深中通道今天通车试运营
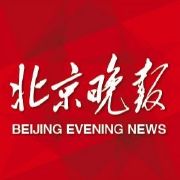
北京晚报
今天上午,深圳至中山跨江通道(以下简称“深中通道”)开通活动在深中通道西人工岛举行,10时50分许,深中通道正式开通。下午3时将通车试运营。作为深莞惠和珠中江两大城市群之间的唯一公路直连通道,深中通道是珠江口A字形交通网络骨架的“关键一横”。深中通道开通后,深圳至中山之间车程从两小时缩短至半小时内,未来广州南沙至中山仅需15分钟,珠海和江门至深圳从2小时以上缩短至1小时内,开创湾区交通发展新格局。
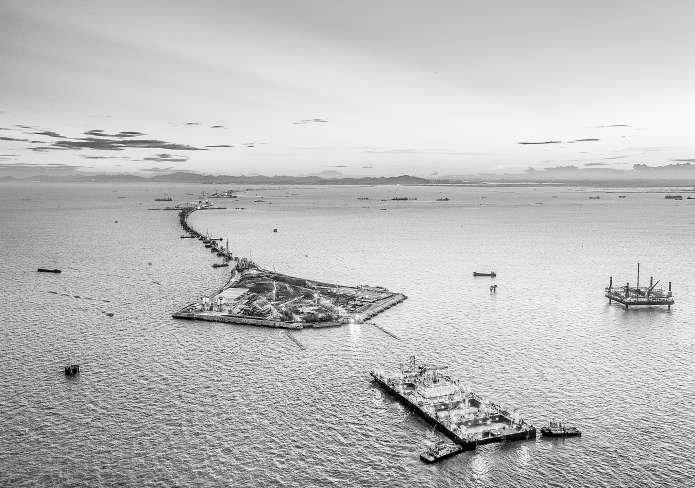
2020年6月16日,深中通道海底沉管隧道首个管节E1浮运至现场等待沉放安装(无人机照片)。
7年筹备,7年建设,深中通道将于6月30日下午3时正式通车试运营。上百家参建单位、上万名建设者为之奉献了时间、汗水和智慧。
深中通道集桥、岛、隧、水下互通于一体,是当今世界上综合建设难度最高的跨海集群工程之一。深中通道全长约24公里,北距虎门大桥约30公里,南距港珠澳大桥约31公里,采用设计时速100公里的双向8车道高速公路技术标准。通车后,从深圳到中山的车程将从目前的2小时缩短至30分钟。
深中通道所在的位置是珠江入海瓶口区域,这里航道密集,建设者们需要找到提高效率的方法来减少施工占用航道的时间。于是他们在原有的工法上推陈出新,研发了DSM硬土层辅助贯入工法。全国水运工程建造大师李一勇说:“我们这个DSM 工法是把硬的变成软的一个过程。”这就好比将原来复杂多样的地质重新组合,加固后形成质地相对均匀的“橡皮泥”,这样,57个钢圆筒就能像没有底的水杯一样平直稳固地插入其中。伴随着最后一个钢圆筒振沉完成,西人工岛围护结构正式形成,全程耗时仅四个半月,比传统的围堰吹填筑岛工法足足节省了一年半的时间。
要保证100年的使用生命周期,锻造出一根根能够承担起如此沉重负担的主缆钢丝是桥梁建设者们需要攻克的难题。要实现这个目标,就要从每一根钢丝开始,向钢丝强度的极限发起挑战。经过三年上百次的反复实验,中国工程师们创新性地在芯铝合金镀层中加入镁元素,使得钢丝的耐久性一下子提高50%,也使得该项技术一举达到了世界先进水平。
7月的一个正午时分,3公里长的猫道上只有几名工人在主缆索股架设现场施工作业。如此重要的施工现场,却几乎不需要人工,这得益于技术团队所开发的智能化远程监控系统。安装在拽拉器上的高清摄像头和传感器,将影像和信号实时传回中枢系统,代替了人工,这使得施工效率得以极大提升。
随着隧道宽度的增加,其自重和受力面积也会随之增加,隧道也就更容易发生弯曲变形甚至损坏。深中通道的海底隧道总长达6.8公里,仅从长度来看就已经是一次空前跨越,而从技术方案和制造施工来看,则是一次质的飞跃。每个管节钢壳由1万多吨钢材打造而成,它就像一件坚实的铠甲,保证了管节在海底的荷载能力和防水性能。
与港珠澳大桥不同,深中通道海底隧道沉管使用的是超宽钢壳混凝土结构,这在国内外都没有先例可以借鉴,因此每一步都需要工程师们反复探索。智能化系统和自动化设备的使用,让一切变得轻松。酷似巨型蜘蛛的智能浇筑机,可以在长165米管节底板和顶板上根据设定的路线自主移动,自动精准寻孔,自主完成整个管节的浇筑作业。
每天超过3000次的凿岩作业,对于锤体和钢丝都是极大的消耗,同样历经千锤百炼的,还有以船为家的工程人员。在海上,为了海底沉管隧道在水下的沉放和顺利对接,工程人员进行的海底隧道基槽开挖工作,整整持续了1400多天。
中国工程师们耗时3年设计并制造了全球首艘集沉管浮运和安装于一体的隧道沉管施工专用船“一航·津安1号”。这个超级装备的横空出世,标志着中国在世界跨海沉管隧道施工领域又实现了一次新的跨越。
深夜航行,海上能见度大幅度降低。中交一航局深中通道项目部常务副总工程师说:“这边加了一套自动巡航,就是它自己驾驶然后跑过去,这样就减少了人为的影响,可以更加安全。它的自动化也是一种大的飞跃。”
2023年6月8日,在31个管节陆续被浮运和安装完成之后,一体船将带着E23管节及最终接头完成最后一次任务。而E23管节及最终接头从结构设计开始就注定成为跨海沉管隧道史上卓尔不凡的存在。整体预制水中推出式最终接头,是一个事半功倍、具有突破性的方案。这得益于钢壳混凝土的沉管结构和沉管钢壳智能化生产线,让世界首例整体预制水中推出式最终接头制造加工,在深中通道项目里成为可能。