守护航天员飞天,神舟十八号舱体加工技术“上新”
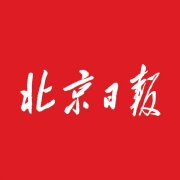
北京日报
转自:北京日报客户端
4月25日,神舟十八号载人飞船成功发射升空。作为航天员实现天地往返的“太空专车”,神舟载人飞船的高密度发射已成为常态。作为神舟飞船重要制造单位,航天科技集团五院529厂神舟飞船研制团队不断升级制造技术,优化科研生产模式,保障飞船舱体按期高质量交付。
截至目前,我国已进行了13次载人飞行任务。随着空间站进入应用与发展工程阶段,神舟飞船的发射任务增加到了1年2艘,密封舱体结构的研制任务大幅增长。
神舟飞船研制团队针对神舟飞船返回舱制造过程中占用产线、设备周期最长的整舱装配加工任务,开发了基于三维投影技术的密封舱大底加工位置诱导技术,解决了返回舱大底在遮挡、变形下蒙皮加工难度大、加工周期长的难题。该方法颠覆了传统工作模式,实现了返回舱大底制造效率和质量的双跨越提升。经验证,新技术较传统方法,加工效率提高5倍,加工精度提高7倍。
“我们最害怕的就是夏天,一旦连续下雨,焊缝质量容易受到影响,加工时间也会拉长。”航天科技集团五院529厂研制人员表示。在多年的研制工作中,神舟飞船团队不断优化生产模式,摸索出了一套适合于组批投产的工作方式,在生产策划阶段做足准备工作,提前抓舱体配套,利用智能软件合理排产,打破以往的单线作战,提前梳理飞船的整体计划,精细化排产,使一些焊接、机加、装配工作形成“微型流水线”,提高了生产效率。
神舟飞船焊接过程中的温湿度控制,对焊接质量而言十分重要,因此,他们在策划焊接周期时,通常会避开或局部改变夏天高湿度等不适宜焊接的自然条件,提前制定舱体焊接生产计划,避免舱体焊接资源冲突,制定了双舱并行的生产模式,确保了每年2艘神舟飞船的快节奏交付进度。
来源 北京日报客户端| 记者 刘苏雅 通讯员 刘淑芬 杨凯 田振 周宓
编辑 匡峰
流程编辑 刘伟利