氢气分离膜研究进展丨中国工程科学

媒体滚动
本文选自中国工程院院刊《中国工程科学》2022年第3期
作者:栾永超,熊亚林,何广利,刘聪敏,李帅
来源:氢气分离膜研究进展[J].中国工程科学,2022,24(3):140-152.
氢气是重要的工业原料和清洁燃料,氢气分离具有重要的经济和社会价值。膜分离法装置结构简单、转换高效、投资成本低且环境友好,在氢气分离领域应用前景广阔;氢气分离膜的性能是影响氢气分离过程效率的决定性因素。
中国工程院院刊《中国工程科学》2022年第3期刊发北京低碳清洁能源研究院高级工程师何广利研究团队的《氢气分离膜研究进展》一文。文章阐述了氢气分离膜的应用需求、基本机理,系统梳理了致密金属膜、无机多孔膜、金属‒ 有机框架(MOF)膜、有机聚合物膜、混合基质膜的研究进展。研究发现,尽管无机多孔膜、有机聚合物膜、混合基质膜等具有良好的氢气分离纯化性能,但在分布式、小型化的应用场景下的分离性能仍待改进提高;提高钯基金属膜的抗毒化性能、优化膜的性价比,是促进工业应用的有效手段;整合无机多孔膜、MOF膜的优点,可促进分子筛分机制膜的性能跃升;有机聚合物膜的耐温、机械等性能仍需提高;对现有高分子膜材料进行改性、制备高分子合金,是开发新型气体分离膜的重要方向;混合基质膜在进行可控调节排布后,将显著提高膜性能。多种氢气分离膜的研究和应用,支撑了氢气分离纯化过程的发展,在材料种类丰富、制备工艺进步后将发挥更大的工程价值。

一、 前言
氢能作为未来能源体系的重要组成部分,将广泛应用于工业、交通运输、建筑供暖等难以脱碳的行业以及其他新兴行业。据中国氢能联盟预测,2060年我国H2需求量将从目前的3.342×107 t/a增加至1.3×108 t/a,在终端能源体系中的占比达到20%。大幅增长的氢能需求对制氢的效率、成本、品质等提出了直接要求,从而驱动制氢技术体系的持续提升。H2纯化技术是制氢 ‒ 用氢的关键环节,主要有物理法、化学法、膜分离法。其中,物理法包括吸附法(变压吸附、变温吸附、真空吸附)、低温分离法(低温精馏、低温吸附);化学法包括金属氢化物分离法、催化法;膜分离法主要涉及无机膜、有机膜、金属膜。
H2纯化方法的应用选择与气源的组成、规模,产品气的品质要求密切相关。例如,对H2供应量大于10 000 Nm3/h的集中大型煤气化、天然气重整制氢,经过变换、脱硫、脱碳后,H2纯化主要采用变压吸附方法。变压吸附法技术成熟,运行成本低、寿命长,但在生产车用燃料电池H2时,因特定杂质去除要求低(如CO≤0.2 ppm(1 ppm=10-6)),以满足杂质含量达标为前提将导致H2回收率和产率明显下降,工艺经济性不足。低温精馏也适用于大规模生产,产品H2纯度一般在85%~99%,同样存在特定场景下无法满足使用要求的问题。对于H2供应量为1000~10 000 Nm3/h的集中副产气制氢,膜分离法所获得H2产品纯度、回收率等与变压吸附法接近,但在装置投资、能耗方面明显低于变压吸附分离、深冷分离等方法。为进一步提高H2产品的纯度和回收率,还可采用有机膜与变压吸附联合工艺。对H2供应量小于1000 Nm3/h的小型分布式现场制氢、车载供氢等应用场景,变压吸附分离存在占地面积大、适应性不佳等问题;金属膜、混合膜等膜分离方法具有装置简单、能量效率高、环境友好等特点,应用前景良好。
膜是膜分离工艺过程的核心。选择合适的材料和制膜工艺,可获得高性能的氢气分离膜,提高产出H2的纯度和产率;降低膜过程的能量消耗,延长膜使用寿命,降低膜工艺的运行成本。提升氢气分离膜技术将促进氢能在诸多领域的大规模应用。随着材料领域的研究发展,出现了更多的氢气分离膜类型:致密金属膜、无机多孔膜、金属 ‒ 有机框架(MOF)膜、有机聚合物膜、混合基质膜(见图1)。目前,针对不同材料类型的氢气分离膜完成了大量的技术攻关工作,材料性能也得到持续改进;但在各类技术发展态势梳理、适用场景分析方面的研究不够充分,不利于精准探讨未来技术发展方向。为此,本文着重梳理氢气分离膜的研究进展,分析各类氢气分离膜面临的技术挑战、解决方法、应用场景优势等,以期为膜技术的发展及研究提供基础参考。
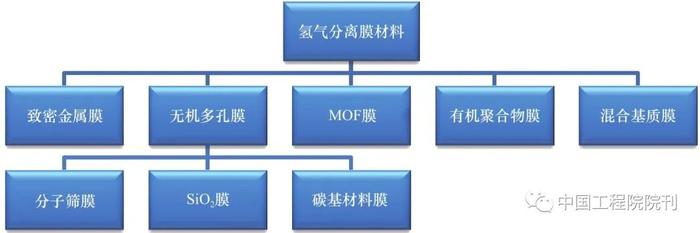
二、氢气分离膜的应用需求
分离膜作为一种高效的气体分离技术,广泛应用于石化、冶炼、环境保护等领域。2021年世界气体分离膜的市场规模约为35亿元,排名前三位的供应商是空气产品公司(美国)、液化空气集团(法国)、宇部兴产株式会社(日本),合计产量占比约为66%。目前商业化应用的膜材料主要是中空纤维膜、螺旋缠绕膜。中空纤维使用最为广泛,约占世界使用总量的89%;用于空气中N2分离、H2分离、天然气中CO2分离、N2/H2O分离等。氢气分离膜技术是开发应用最早、技术最成熟的气体膜分离技术之一,第一种工业化的气体分离膜是用于H2/N2分离的聚砜中空纤维膜。20世纪80年代初,中国科学院大连化学物理研究所在国内率先研制中空纤维H2/N2分离膜。
我国适宜发展的制氢工艺类型多样,天然气重整、煤气化是目前获取H2的主要方法。制氢过程中生成中间产物转化气(CO、H2),其中CO通过水煤气变换反应进一步与水蒸气反应,因此气体产品中主要成分为H2、CO2,还有少量杂质气体如CO、CH4。通过农业废弃物等生物质材料也可制取H2,由于有机物中碳元素的存在,所得H2产品中也含有一定量的CH4、CO、CO2。在合成氨、合成甲醇的生产过程中,为提高反应效率而产生一定量的含氢驰放气。合成氨驰放气、合成甲醇驰放气均具有压力高、H2浓度低的特点,H2含量不高于50%,其余组分主要是难以分离的惰性气体(如N2、Ar)。水电解制备的H2纯度一般在99.5%~99.8%,H2中含有O2、水蒸气等。
不同制氢方式含有的杂质气体种类不同,而各类应用场景对H2的纯度要求不同。在化工领域,主要以H2的浓度来划分品质等级,如纯氢(≥99.99%)、高纯氢(≥99.999%)、超纯氢(≥99.999 9%)。在交通领域,以燃料电池汽车为例,不仅规定了H2纯度≥99.97%,同时规定了CO、总硫等14类杂质的限值。虽然有机高分子膜材料仍是今后一段时期内氢气分离过程的主要膜材质,但选择性问题限制了其在高纯H2制备过程中的应用。新型无机膜材料的不断涌现,为气体纯化应用打开了想象空间。
在我国,气体膜分离研究偏重材料开发,而在组件、装置、过程优化等方向投入不足。在低碳制氢发展趋势下,为了满足不同分离场景需求、促进气体膜分离技术的应用和发展,需要深入开发膜材料品类、特异性功能聚合物膜材料分子设计、膜超薄化技术优化、膜分离法与其他分离方法耦合技术,以材料、组件、装置、工艺仿真的全面突破来实现膜技术体系革新。
三、氢气分离膜机理
利用膜来分离气体的基本原理是:在混合气体中,不同组分在压力的驱动下具有不同的透过膜速率;传递速率高的组分在透过侧富集,传递速率低的组分在原料侧富集,从而实现混合气体分离的目的。气体分子在膜中的传递机理涉及黏性流、努森扩散、表面扩散、毛细管凝聚、分子筛分、表面扩散、溶解扩散、促进传递(见图2)。

当气体分子平均自由程远大于膜孔径时,气体在膜中以黏性流机理传递;孔隙内分子流动在很大程度上受到分子之间碰撞作用的影响,气体分子的传递不受气体种类的影响,因此不能实现混合气体的分离。当气体分子的平均自由程远大于膜孔径时,气体分子与孔壁碰撞的概率大于分子之间的碰撞概率,气体分子与孔隙壁间的碰撞起主导作用;气体分子通过努森扩散机理传递,气体通过膜孔流量与气体相对分子质量的平方根成反比,分离系数与气体相对分子质量比值的平方根成反比。由分子传递机理可见,对于黏性流、努森扩散状态,难以实现有效分离;应尽量避免气体分子在分离膜中依据这两种传递机理进行传递。
分子吸附在孔壁上将沿孔壁表面移动,产生表面扩散流;通常沸点低的气体易被孔壁吸附,表面扩散显著;操作温度越低、孔径越小,表面扩散越明显。当混合气体中的组分在膜表面发生物理吸附、在膜孔内发生毛细管冷凝时,膜孔将会被堵塞,造成非冷凝组分无法通过;孔道内的冷凝组分流出孔道后蒸发离开膜面,从而实现混合气体的分离;不同气体在冷凝温度上存在差异,可依据毛细管冷凝原理实现分离。
当膜孔径介于混合气体各组分的分子直径之间时,直径小的分子可以通过膜孔,直径大的分子则被截留;由此产生筛分作用,实现气体分离。基于溶解扩散机理的膜,对混合气体中某种组分的溶解性高、对其他组分的溶解性低,由此通过对不同组分的选择性溶解而达到分离目的。气体与溶解后的选择性膜接触,溶解在膜表面;分子在膜两侧浓度梯度的作用下向前扩散,到达膜的另一侧后解离。促进传递机理发生在具有载体的膜中,在膜内引入载体后,通过载体与混合气体中某一特定组分之间发生可逆的相互作用,促进该组分从膜表面向另一侧传递。
特定气体分子透过某一特定的分离膜,相关过程较为复杂,通常是一种或多种传递机理共同作用的结果。因此,气体分子透过某一特定的分离膜可依据一种或多种传递机理。特定的气体分子在膜内的传递机理涉及三方面:气体分子自身的理化性质、膜的结构、气体分子与膜材料之间的相互作用。H2在膜内的传递,主要依据分子筛分、溶解 ‒ 扩散机理。
四、氢气分离膜的研究态势分析
氢气分离膜可分为氢气透过膜、杂质气体透过膜两类:前者允许H2透过而截留杂质气体,使H2在渗透侧富集而实现分离;后者使H2在原料侧富集,从而分离混合气体。目前,氢气分离膜多为氢气透过膜类型,这是因为H2分子是除He、H2O分子以外动力学直径最小的分子,扩散速率高,容易渗透通过膜。
(一)致密金属膜
1. 致密金属膜分类
致密金属膜是最常用的氢气分离膜,Ni、Pd、Pt以及元素周期表中第三族至第五族的金属都能透过氢。致密金属膜对于H2具有优良的选择性和渗透性,应用前景广泛,但实际工业应用仍面临各种挑战,如膜的热稳定性、机械性能有待提高,差的化学稳定性、易被杂质气体毒化、高的制备成本也限制了应用规模扩大。H2在致密金属膜中遵循溶解 ‒ 扩散机理,步骤为:氢分子扩散到膜表面,氢分子解离吸附在表面,氢原子溶解在膜基体材料中,氢原子在膜材料中扩散,氢原子在膜背面重新结合生成氢分子,氢原子从膜背面脱附,氢分子扩散离开膜。
在由单一元素组成的纯金属膜中,H2渗透性能取决于金属的晶格结构、化学反应性、晶格缺陷。首先是以第五族元素(如Nb、Ta、V)和α-Fe为体心的立方结构,具有较高的H2渗透性。其次是面心立方结构(相关元素为Ni、Pd、Pt等)得到较多的关注和研究,其中与Pd相关的结构表现出相对高的H2渗透性。尽管相比于Pd,Nb、Ta、V的H2透过性能更好,但Nb、Ta、V易与H2生成稳定的氢化物,所出现的氢脆现象将破坏材料的机械性能;相对于H2的扩散速率,第四族和第五族金属(如Nb、Ta、V)催化氢分子解离与重新结合的速率过低,也会在表面生成致密的氧化物,可能抑制氢分子在金属中的解离和吸附。为了提高单一金属的物理特性(如强度、稳定性、抗老化性)并保持较高的H2渗透性,通常加入其他元素形成金属晶体合金;例如,基于第四族(Zr、Ti、Hf)和第五族(V、Nb、Ta)元素的合金具有较高的H2渗透性能。Ti、Co、Cr、Al常用于制备金属合金,Fe、Mn、Mo、Cu、Ni、Ga、Ge、Sn、Si、W、La、Be等也是可用元素。
在多种金属的膜中,Pd及其合金膜长期以来获得广泛关注和深入研究,采用Pd及其合金膜纯化后,H2纯度可达99.999 99%。阻碍纯Pd膜应用的突出问题是氢脆现象,即当温度低于300 ℃、压力低于2 MPa时,Pd存在α相与β-氢化物相转变,晶格之间产生应力,出现缺陷。Pd膜在接触硫化物、CO、H2O等物质时会发生中毒现象,严重降低H2渗透性能。为了避免Pd膜的氢脆、中毒现象同时降低膜的成本,多在Pd中掺入其他元素(如Fe、Cu、Ni、Ag、Pt、Y)形成合金膜。
2. Pd及其合金膜的制备方法
Pd及其合金膜的制备方法主要分为化学镀、化学气相沉积、物理气相沉积、电沉积等,在实际应用过程中可根据具体条件选择适用方法。
① 化学镀通过还原剂将金属离子还原,形成金属薄层并作为催化剂促进后续反应进行。在化学镀过程中,首先通过敏化、活化、在支撑材料表面引入Pd前驱体颗粒,然后形成Pd层。Shigeyuki等首次使用化学镀制备了Pd及其合金膜,成为制备Pd膜最常用的方法。化学镀易于成膜、成本低、设备简单,但也存在操作复杂、消耗时间长的问题。
② 化学气相沉积通过热分解不稳定前驱体来制备Pd分离层,可调控厚度。Ye等使用PdCl2作为金属来源制备了Pd膜,开启了Pd制备方向的应用。与化学镀相比,化学气相沉积可制备更薄的Pd及其合金膜(最小厚度可至2 μm),但是需要前驱体具有较高的挥发性和热稳定性。
③ 物理气相沉积在真空条件下,通过高能电子束或离子束将材料源气化成气态原子级粒子,后沉积形成薄膜;与化学气相沉积类似,不涉及化学分解反应(前驱体为纯金属所致)。
④ 电沉积指金属或合金从其化合物的液相体系中电化学沉积的过程,在这一过程中金属或合金沉积在电极上。电沉积设备简单、易于成膜,膜的厚度可通过调节时间或电流来改变;但只能将薄膜沉积在导电性材料(如不锈钢)上,使用范围存在局限性。
3. Pd及其合金膜基底材料
Pd及其合金膜主要分为自支撑膜、具有支撑层的膜两类。自支撑膜没有基底支撑,膜的不同部位材料相同,通常为片状或管状结构。早期的自支撑管式膜壁厚度约为100 μm,较厚的管壁可提高H2分离纯度,但H2渗透性能较低,昂贵的造价限制了应用范围;目前在小规模H2纯化、研究性应用中,为了评价Pd及其合金材料的本征特性,相关方法仍有应用。为了具有足够的机械性能,自支撑膜的厚度一般不小于20 μm,相应的H2渗透速率较低(1.4×10-8~9.3×10-7mol/(m2·s·Pa))。Mckinley采用化学镀制备了厚度为25 μm的Pd膜、Pd60Cu40膜:前者的H2渗透速率为4.58×10-7 mol/(m2·s·Pa),后者的渗透速率达到7.56×10-7 mol/(m2·s·Pa)。采用合适的方法降低管壁厚度(小于20 μm)可兼顾膜的性能和经济性。Gade等制备了厚度为7.2 μm的Pd膜,H2渗透速率为1.56×10-6 mol/(m2·s·Pa),H2/N2分离因子大于40 000;在相同制备条件下,当膜厚度增大至14.6 μm时,H2渗透速率下降为5.5×10-7 mol/(m2·s·Pa),H2/N2分离因子下降为205;制备了厚度为16.7 μm的Pd59Cu41膜,H2渗透速率为1.01×10-6 mol/(m2·s·Pa),H2/N2分离因子为105。
具有支撑层的膜通常是在多孔基底上沉积Pd或其合金超薄层以形成复合膜;基底提供机械强度,Pd或其合金超薄层提供选择渗透性能。基底的性质可影响Pd或其合金超薄层的结构及性能,常用的基底有维克玻璃、陶瓷、不锈钢。维克玻璃由SiO2、B2O3、Na2O、Al2O3构成,通过稀酸溶液处理使硼溶出,得到孔径为4~300 nm的多孔结构;具有良好的热稳定性,但机械性能较低。维克玻璃是最先应用于制备Pd复合膜的基底。Uemiya等在多孔玻璃基底上通过化学镀制备了Pd、Pd94Cu6、Pd93Ag7超薄层,H2在复合膜中的渗透速率为2×10-7~9.6×10-7 mol/(m2·s·Pa),渗透侧检测不到N2(即H2/N2分离因子极大)。Altinisik等通过化学镀在多孔玻璃基底表面沉积了厚度为15 μm的Pd层,473 K、11 kPa测试条件下的H2渗透速率为2.6×10-5 mol/(m2·s·Pa),但H2/N2分离因子(7)仅稍大于努森扩散分离因子(3.7),这可能是因Pd层存在缺陷所致。为了增加Pd与多孔玻璃之间的亲和性以防止出现缺陷,Kuraoka等在真空状态下将Pd嵌入维克玻璃的孔中,所得复合膜的H2渗透速率与基底相同(在723 K测试条件下为4.9×10-8 mol/(m2·s·Pa)),高于采用传统方法在玻璃基底表面沉积Pd层所制的复合膜;相应的H2/N2分离因子为520,远高于传统方法所制膜。
多孔陶瓷基底是一类应用广泛的非金属材料,其中Al2O3因其机械稳定性和热稳定性良好,常用作Pd复合膜的基底。基底表面性质(如孔径分布、粗糙度等)对Pd或合金层的生长影响明显。为了避免出现缺陷,应选择基底孔径分布均匀、表面突起不超过超薄层厚度的基底来制备复合膜。Zhang等采用真空化学镀在Al2O3基底表面沉积Pd超薄层,753 K、100 kPa测试条件下的H2渗透速率为2.6×10-6 mol/(m2·s·Pa),H2/Ar分离因子为2100。Itoh等采用化学气相沉积在管状Al2O3基底表面沉积Pd超薄层,573K、30 kPa测试条件下的H2渗透速率为3.3×10-6~6.7×10-6 mol/(m2·s·Pa),H2/N2分离因子约为5000。
Zhao等在管状陶瓷基底的内外表面分别沉积Pd超薄层(防止吹扫气进入基底影响分离效率),Pd / 陶瓷 / Pd膜与传统Pd / 陶瓷膜的Pd厚度几乎相同,两者H2渗透速率相差不大(100 kPa、773 K测试条件下的H2渗透速率为2×10-6 mol/(m2·s·Pa)),前者的H2/N2分离因子为14 429,后者为4832。Melendez等采用化学镀在管状Al2O3载体上负载Pd/Ag超薄层来制备复合膜,100 kPa测试条件下的H2渗透速率为9×10-6~9.4×10-6 mol/(m2·s·Pa),H2/N2分离因子为2000~3300。
多孔陶瓷基底表面结构对Pd超薄层的形成具有明显影响。除了在基底上直接沉积Pd超薄层,可以在基底和Pd之间引入中间层,如Guo等在Al2O3基底上先生长Sil-1分子筛层、后沉积Pd,773K、100 kPa测试条件下的H2渗透速率为1.78×10-6 mol/(m2·s·Pa),H2/N2分离因子为1500。还可通过后处理将中间层去除,赋予膜的特殊性能,如Tong等先将聚合物层覆在载体表面,后将Pd沉积在有机聚合物层上,再经高温处理除去聚合物层,最后得到Pd复合膜(见图3);773 K、100 kPa测试条件下的H2渗透速率为3.3×10-6 mol/(m2·s·Pa),He无法透过膜,H2/He分离因子极大。这是因为,聚合物层致密光滑,Pd在其表面均匀分布形成无缺陷的薄层;移除聚合物层后,Pd与基底之间的缝隙可为Pd在高温下的膨胀提供足够空间,使其在高温下保持较高的性能。

多孔金属因与Pd具有相似的热膨胀系数而成为一种性能良好的基底。不锈钢易于加工、化学稳定性好、价格低廉,是常用的金属基底材料。商品不锈钢基底的孔径最小为0.2 μm,较大的孔径、孔径分布的不均匀性导致了基底表面粗糙度的不均匀;为了防止因孔径、粗糙度导致Pd超薄层出现缺陷,通常采用机械处理、打磨表面、热处理、预沉积中间层等方式来减小基底孔径。Tong等在Al2O3凝胶修饰的不锈钢基底上,通过化学镀制备Pd或Pd/Ag超薄层,所得复合膜在673~773 K、100 kPa测试条件下的H2渗透速率为1.7×10-6 mol/(m2·s·Pa),He无法通过该膜。Nam等在孔径为500 nm的不锈钢片基底上,先填充Ni粉末提高基底平整性,后通过电沉积法在表面形成Pd/Ni超薄层(Ni粉末还在一定程度上提高了基底和Pd/Ni超薄层的亲和性),制备的不锈钢支撑Pd合金膜在723 K测试条件下的N2渗透速率为6.7×10-6 mol/(m2·s·Pa),H2/N2分离因子为3000。Kim在Al2O3修饰的不锈钢基底上通过化学镀沉积了Pd/Ru超薄层来制备复合膜,723 K、100 kPa测试条件下的H2渗透速率为8.4×10-7 mol/(m2·s·Pa),H2/He分离因子为1150;所制备的膜具有一定的耐受性,经HCl、SiHCl3气体破坏后的9 h,在498 K、200 kPa测试条件下H2通量保持在2.0 m3/(m2·h)左右,仍保持较好的性能。
(二)无机多孔膜
1. 无机多孔膜分类
能够实现气体分离的无机多孔膜,其孔径通常小于2 nm,鉴于H2渗透机理一般为分子筛分,因而孔径的孔型成为决定无机多孔膜分离性能的重要因素。根据膜材料种类,无机多孔膜分为分子筛膜、SiO2膜、碳基材料膜。由于无机多膜孔材料的孔道结构对分离性能至关重要,在基础研究方面需着重阐明膜分离的构效关系。通过精细设计、有效调控等方式制备可控尺寸、分布均一的无机膜材料,是未来发展方向。在追求高分离性能的同时,综合考虑规模化制备膜的可行性、经济性、稳定性等因素。
2. 分子筛膜
分子筛膜主要由硅酸盐、磷酸铝、硅磷酸铝形成,具有良好的机械性能、较高的化学与热稳定性。由于无法制备分子筛自支撑膜,分子筛膜较多采用多孔基底作为支撑层以提供必要的机械强度,常用的基底有Al2O3、多孔金属。立方晶体(LTA)型分子筛膜应用最为广泛,Na-LTA型分子筛膜因其孔径最小(约4 Å)而在理论上适用于基于分子筛分原理的混合气体分离过程。通过离子交换处理可得孔径为3 Å的K-LTA型分子筛膜,可用于分离H2/CO2体系。也要注意到,LTA型分子筛膜存在较多的晶格间缺陷(尺寸为1~2 nm),造成CO2等杂质气体也可快速通过。为此,Huang等采用偶联剂提高分子筛层与多孔基底之间的结合力,在维持H2渗透性能的同时显著提高了分离性能;以3-胺丙基三乙氧基硅烷作为偶联剂,在293 K条件下测试二元混合气体,H2渗透速率为3.0×10-7 mol/(m2·s·Pa),H2/CH4、H2/N2、H2/O2、H2/CO2选择性分别为3.6、4.2、4.4、5.5;以3-氯丙基基三甲氧基硅烷作为偶联剂,293 K、100 kPa测试条件下的H2渗透速率为2.2×10-7 mol/(m2·s·Pa),二元混合气体测试中的H2/CO2、H2/N2、H2/CH4、H2/C3H8、H2/C3H6选择性分别为7.4、6.8、5.3、15.3、36.8。
具有双十元环交叉孔道结构(MFI)型膜是另一种常见的分子筛膜,因其孔径为5.6 Å而无法获得较高的H2分离性能,可通过甲基二乙氧基硅烷催化裂化沉积法来减小膜孔径。Tang等据此可控减小了MFI型分子筛膜的孔径,在提高膜选择性的同时保证了较高的H2渗透速率;在723 K、150 kPa条件下测试二元混合气体,H2渗透速率为3.96×10-7 mol/(m2·s·Pa),H2/CO2选择性为141。
不同于分子筛膜,SiO2膜多为无定型结构,易于形成多孔超薄分离层,具有优异的分子筛分性能。Duke等采用传统前驱体正硅酸乙酯制备多孔SiO2,通过正电子湮灭测试其自由体积;发现SiO2的孔径为3.0 Å(H2、CO2、N2、CO等的动力学直径分别为2.89 Å、3.3 Å、3.64 Å、3.76 Å),适用于H2分离和纯化。SiO2膜在H2分离纯化领域得到较多研究。Gu等在具有梯度结构的Al2O3基底上构建了厚度为20~30 nm的SiO2超薄分离层,所得复合膜表现出较高的H2/CO2分离性能和H2渗透速率,873 K、100 kPa测试条件下的H2渗透速率为5×10-7 (m2·s·Pa),H2/CH4、H2/CO、H2/CO2选择性分别为5900、5100、1500。
3. 碳基材料膜
碳基材料膜中最常见的是无定型多孔碳分子筛膜,通常是在真空或惰性气体保护环境下,将聚糠醇、聚丙烯腈、酚醛树脂、聚酰亚胺等聚合物前驱体碳化或热解制备而成。聚合物在碳化过程中发生分子链断裂,生成的小分子以气体形式逸出,气体逸出时的通道形成了多孔结构。膜中较大的孔(0.6~2.0 nm)由较小的孔连接,从而赋予膜较好的筛分性能和渗透性能。碳分子筛膜的形式分为自支撑膜、基底支撑复合膜:前者多是中空纤维膜,具有装填密度高的优点;后者的机械强度获得明显提高,具有更为广泛的应用潜力。复合膜制备时,需采用刮刀涂覆法、旋转涂覆法、浸涂法等,将聚合物涂覆在基底上;基底的性质(如孔结构、表面粗糙度)对形成无缺陷碳分子筛膜具有重要影响;多次涂覆 ‒ 碳化可有效避免缺陷的形成,但会导致分离层厚度增加、气体渗透速率降低。为了提高分离层与基底之间的亲和力、促进分离层的均匀性,Li等在基底表面引入有序介孔碳以改善表面性质,随后涂覆聚合物层并碳化制备碳分子筛复合膜;获得较高的气体选择渗透性能,室温、100 kPa测试条件下的H2、CO2、O2、N2渗透速率分别为5.455×10-5 mol/(m2·s·Pa)、8.8×10-6 mol/(m2·s·Pa)、7.45×10-6 mol/(m2·s·Pa)、7.15×10-7 mol/(m2·s·Pa),H2/N2、CO2/N2、O2/N2选择性分别为76.3、12.3、10.4。
石墨烯膜是一种新型的碳膜,有望实现工业应用。石墨烯为单分子层结构且表面光滑,易于获得较高的渗透速率,兼具良好的机械性能和化学稳定性。然而,石墨烯的方向环可阻挡分子从其中通过,单片完整的石墨烯并无渗透性能,常用的应对方法有两种(见图4):在石墨烯片上打孔;将石墨烯组装成层状结构,形成二维纳米通道。有多种物理或化学方法可用于在石墨烯片上打孔,如氧化刻蚀、激光辐照、氦离子轰击、电子束辐射、蒸汽刻蚀。Koenig等采用紫外线诱导氧化刻蚀法在石墨烯片上打孔,H2、CO2、Ar、N2、CH4在孔中的透过速率分别为4.5×10-23 mol/(s·Pa)、2.7×10-23 mol/(s·Pa)、2×10-26 mol/(s·Pa)、3×10-27 mol/(s·Pa)、3×10-27 mol/(s·Pa),因此该膜可实现H2/N2、H2/CH4、H2/CO2等的分离。此外,通过数值模拟可预测石墨烯的表面孔径,如Jiang等计算得出氮原子功能化的孔尺寸为3.0 Å×3.8 Å,而全氢原子钝化的孔尺寸为2.5 Å×3.8 Å,对H2/CH4混合气体的选择性可达1×108。需要指出的是,虽然石墨烯片打孔在分离性能方面表现出良好潜力,但是在精密控制、大面积制备、组装为实际膜组件等方面仍存在很多技术难题。
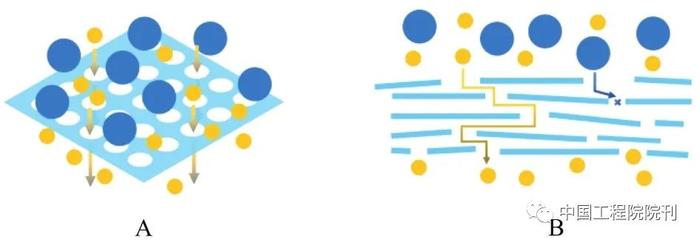
石墨烯材料自身不可避免地会出现缺陷,利用这些缺陷也可实现混合气体的分离,如Yu等采用真空过滤法在Al2O3基底上自组装超薄石墨烯分离层,在273 K条件下测试二元混合气体,H2渗透速率为1×10-7 mol/(m2·s·Pa),H2/CO2、H2/N2选择性分别为3400、900。此外,可将微观石墨烯片组装成宏观结构,形成二维通道。在多孔基底上自组装石墨烯片是制备实用型石墨烯膜的常用方法。Kim等采用两种方式分别在聚醚砜基底上通过旋涂法组装石墨烯层:将基底与石墨烯分散液表面接触,将石墨烯分散液直接滴在基底表面;在293 K、100 kPa测试条件下,第一种方法所制膜的H2渗透速率为1.2×10-8 mol/(m2·s·Pa),H2/CO2选择性为30,第二种方法所制膜的CO2渗透速率大于H2渗透速率。利用石墨烯与水之间的亲和性以及CO2在水中的高溶解性,可使CO2在膜中优先透过,由此实现CO2/H2混合气体的分离。
(三)金属 ‒ 有机框架膜
MOF是一种有机 ‒ 无机杂化多孔固体材料,几何和晶型结构规整,由金属离子或金属离子簇以及有机链段构成。作为一种新型多孔材料,MOF膜材料以其高孔隙率、大比表面积、孔尺寸高度可调、结构多样的特点展示出良好的H2分离效果。然而,MOF材料本身仍然处于实验室研发阶段,稳定性不佳的问题需要解决;将MOF材料与其他功能材料进行复合,可在保证吸附分离性能的同时提升MOF材料的结构稳定性,这是MOF膜材料后续的发展方向。
Liu等首次将MOF膜用于气体分离领域,在Al2O3基底上负载MOF层以形成表层连续无缺陷的MOF-5复合膜;单组分气体在MOF-5膜中以努森扩散机理传递。Guo等制备了以铜网为基底、Cu3(BTC)2为分离层的MOF膜(即“双铜源”),在298 K、100 kPa条件下测试H2/N2、H2/CH4、H2/CO2等二元混合气体,H2渗透速率为1×10-6 mol/(m2·s·Pa),H2/N2、H2/CH4、H2/CO2选择性分别为7、6、6.8;测试结果远超努森扩散机理的理论值,表明这种膜具有较高的H2分离能力。
原位生长、二次生长是制备MOF膜的常用方法。原位生长过程中基底与生长液接触,成核和生长同时在基底表面进行。Bux等通过微波辅助溶剂热合成法在TiO2基底上生长ZIF-8层,生成MOF膜;测试H2的渗透速率为6.04×10-8 mol/(m2·s·Pa),测试H2/CH4二元混合气体的H2渗透速率为5.08×10-8 mol/(m2·s·Pa),表明该膜具有较高的H2渗透速率和分离性能。为了抑制MOF膜中缺陷的生成以提高分离性能,Kang等在镍网上原位生长MOF,镍网不仅提供机械支撑,而且作为单一镍源与有机物结合形成连续MOF层;该反应为自抑制过程,使得生成的MOF层薄且无缺陷。Huang等通过原位生长法在多巴胺修饰的Al2O3基底上构建ZIF-8层以制备MOF膜,通过层层自组装法在膜表面沉积石墨烯片;由于毛细管和共价键的作用,石墨烯片仅存在于ZIF-8晶体之间的缝隙中,因而气体只能通过ZIF晶体中的空隙传递;在553 K、100 kPa条件下,测试H2/CO2、H2/N2、H2/CH4、H2/C3H8二元混合气体的H2渗透速率分别为1.27×10-7 mol/(m2·s·Pa)、1.34×10-7 mol/(m2·s·Pa)、1.29×10-7 mol/(m2·s·Pa)、1.29×10-7 mol/(m2·s·Pa),H2/CO2、H2/N2、H2/CH4、H2/C3H8选择性分别为14.9、90.5、139.1、3816.8;这表明,在保证较高H2渗透速率的前提下,显著提高了膜对混合气体的分离性能。
二次生长法将MOF晶体成核和生长过程分开进行,更易获得连续无缺陷的膜且膜结构易于调控。成核过程对二次生长法制备无缺陷膜具有重要影响,决定了MOF层与基底之间的结合力。Yoo等在二次生长制备MOF膜过程中,采用微波辅助MOF成核,形成与基底具有强结合力的晶体;较高的微波能量使基底表面温度升高,有利于成核过程的快速进行,测试单组分H2的渗透速率为8×10-7 mol/(m2·s·Pa),CO2、N2、CH4的渗透速率介于2×10-7~4×10-7 mol/(m2·s·Pa)。Nan等采用分步成核法制备MOF膜,在298 K、100 kPa条件下测试H2/CH4、H2/N2、H2/CO2二元混合气体的H2渗透速率分别为5.16×10-7 mol/(m2·s·Pa)、4.79×10-7 mol/(m2·s·Pa)、6.74×10-7 mol/(m2·s·Pa),H2/CH4、H2/N2、H2/CO2选择性分别为3、3.7、4.6。Lee等采用分步成核法制备MOF膜,298 K、100 kPa条件下测试的H2渗透速率为1.27×10-6 mol/(m2·s·Pa),H2/N2、H2/CO2、H2/CH4选择性分别为3.1、9.1、2.9。
(四)有机聚合物膜
1. 有机聚合物膜分类
有机聚合物膜易于制备、调控且价格低廉,具有较高的商业价值,常见种类为致密膜;气体在膜中按照溶解 ‒ 扩散机理传递,上游气体吸附并溶解在膜中,后在推动力作用下从膜的一侧向另一侧扩散,透过膜后从膜上脱附。气体的传递性能由其在膜中的溶解、传递性能共同决定。H2具有较小的动力学直径,而CO2、CH4等气体等更易于压缩;从热力学角度看,H2优先透过;从动力学角度看,CO2、CH4等气体优先透过。这种竞争作用使得制备基于溶解 ‒ 扩散基质的高选择性有机聚合物氢气分离膜较为困难。对于氢气渗透膜,强化材料渗透性并弱化溶解性是获得高性能的有效方法。玻璃态聚合物是常见的氢气分离膜材料,具有刚性结构、窄的自由体积分布,可形成类似分子筛分机制的无机膜。代表性的氢气分离膜材料有聚酰亚胺、聚苯并咪唑及其衍生物,作为新型膜材料的热重构聚合物也受到更多的关注。鉴于成本较低、易于制备、可加工性好等优点,有机聚合物膜材质仍是今后一段时间内氢气膜分离过程的主要膜材质。有机聚合物膜因自身结构特性,很难同时具备较高的气透性与选择性,这是未来研究需要着力解决的问题。将无机、高选择性的材料混合到聚合物膜中,提高聚合物的选择性和处理能力,改善耐高温、抗化学腐蚀性能,成为有机聚合物膜材料的主要发展方向。
2. 聚酰亚胺膜
聚酰亚胺具有良好的分离性能和稳定性,适用于制备分离膜。基于六氟二酐的聚酰亚胺是应用广泛的气体分离膜材料,但膜的选择性较低,无法满足H2分离需求。通常采用后处理过程以增强膜性能,聚酰亚胺交联是常用的后处理方法。Low、Shao等采用二胺或三胺如二胺基丙烷、乙二胺、二亚乙基三胺等交联聚酰亚胺,构建了聚酰胺聚合物网状物。在早期工作中,将膜浸入胺溶液进行交联,虽然提高了H2/CO2离性能,但是H2渗透性明显下降;膜在溶剂中由于不均匀溶胀,形貌易受破坏。为了提高H2渗透性能、保障膜的形貌完整性,发展了气相交联法,即膜表面与交联剂蒸气接触,反应仅发生在膜表面;在改变膜表面高分子结构以提高选择性的同时,不改变本体结构(确保膜的机械性能)。采用气相交联法实现了二乙胺修饰六氟二酐 ‒ 四甲苯聚酰亚胺膜,在350 kPa条件下测试的H2渗透速率为1×10-9 mol/(m2·s·Pa),H2/CO2选择性为102,测试H2/CO2混合气体的H2渗透速率为6×10-10 mol/(m2·s·Pa),H2/CO2选择性为16.6。
3. 聚苯并咪唑及其衍生物膜
苯并咪唑因具有刚性棒状分子结构表现出优异的热稳定性和机械稳定性。聚(2,2’-间苯二胺-5,5’-苯并咪唑)(PBI)是最为典型的苯并咪唑聚合物。大量研究指出,由于分子内强的氢键作用和链段刚性,PBI膜能够将H2从多种混合气体中有效分离出来。Berchtold等在负载有ZrO2中间层的不锈钢基底上制备了复合膜,组装成管式膜组件;在523 K条件下测试,H2渗透速率为2.3×10-9 mol/(m2·s·Pa),H2/CO2、H2/CH4选择性分别为47.6、233.6。Li等合成了一系列主链结构不同的PBI衍生物,通过分子结构修饰来调控链段堆积状态与自由体积,从而提高PBI膜的渗透性能;在523 K、345 kPa条件下测试的H2渗透速率介于1.2×10-9~5.4×10-8 mol/(m2·s·Pa),H2/CO2理想分离因子范围为5.174~23.03,H2/N2选择性范围为18.72~98.32,H2渗透速率和分离因子呈负相关。
4. 热重构聚合物膜
在多孔材料、共价有机框架、热重构聚合物、自聚微孔聚合物等多种新型材料中,热重构聚合物前驱体(主要为功能化聚亚酰胺)因其可溶性、易于加工,可制备成膜用于气体分离。Park等提出基于固体热转换的热重构理论,对于玻璃态的刚性聚合物链段,改变空间排布来调控孔径及其分布,实现了分子级的高性能分离膜构建。热重构聚合物双峰孔径分布特性为:大孔负责快气运输,小孔负责基于尺寸差异的气体分离;由聚酰亚胺前驱体生成的热重构聚合物,H2分离方向的渗透选择性良好。Han等制备了苯并咪唑热重构膜,渗透系数为4.194×10-7 cm3 (STP)·cm/(cm2·s·cmHg)时的H2/N2、H2/CH4选择性分别为15、28。除了实验研究,还可通过模拟计算考察热重构聚合物膜的分离性能。Park等认为通过模拟方法计算的热重构聚合物气体溶解、扩散、渗透性能,与实验值具有高度的关联性,体现了模拟方法的可靠性。
(五)混合基质膜
混合基质膜指将有机和无机材料掺杂而成的膜,通常有机聚合物作为连续相,无机材料作为分散相;不仅可以弥补聚合物膜和无机膜的不足,而且能够联合两者优点(如聚合物良好的加工性能、无机材料的高气体分离性能)。因此,混合基质膜在气体分离领域得到广泛应用。大量无机材料以及聚合物的存在与发展,为设计先进的混合基质膜提供了更多的可能性。也要注意到,填料与基质之间的相容性问题是制约混合基质膜发展的重要因素,因而实现有序掺杂是提高混合基质膜材料性能的重要方向。
理想的混合基质膜要求无机材料在有机聚合物中均匀分散,且添加量尽可能地多。但实际应用中的一些问题,如非选择性界面孔隙、链段僵化、孔隙堵塞,限制了无机材料的添加量。为了获得高选择渗透性能的氢气分离膜,玻璃态聚合物、具有分子筛分功能的无机材料进行组合是优化选择。较多采用的有机聚合物为聚酰亚胺和聚(2,2’-间苯二胺-5,5’苯并咪唑),初期使用的无机材料有SiO2、分子筛等。Joly等制备了聚酰亚胺 / SiO2混合基质膜,相应的H2、CO2、CH4等气体渗透性能有所改善,对H2的选择性也有明显提高。Sen等制备了聚碳酸酯 / 4A分子筛混合基质膜,具有较高的H2渗透性和选择性,如H2/N2、H2/CH4选择性分别为73.2、70.4。MOF在混合基质膜方向具有极大潜力。Ordonez等开发了掺杂有ZIF-8的混合基质膜,ZIF-8添加量为50%时的H2/CH4选择性从121提高到472。
五、结语
H2是我国石油化工领域的重要原料,以较低能耗获取低成本、高纯度的H2是行业降本增效、提高市场竞争力的重要手段。我国已将氢能定位于未来能源体系的重要组成部分,后续氢能应用领域必然更为广阔,随之而来的是氢能供应品质的更高要求。氢气分离膜相对于变压吸附、低温冷凝、深冷分离等方法,投资成本较小、低能耗、易扩展,在诸多行业均有极大的应用空间(尽管不同应用需求对膜材料性能要求不尽相同)。多种氢气分离膜的研究和应用,促进了H2分离纯化过程的发展,将在H2分离领域展现更大应用价值。
目前,虽然各类氢气分离膜如无机膜、有机膜、混合基质膜等,均表现出良好的H2分离纯化性能,但对照分布式、小型化的应用场景需求,氢气分离膜技术体系仍有待提高。
① 在无机膜中,Pd基金属膜的贵金属特性导致制膜成本高,制约了工业应用规模。进一步提高Pd基金属膜的选择渗透性能并改善性价比,是促进工业应用的有效手段。对于无机多孔膜,分离性能受到孔径及其分布的影响;MOF膜具有窄的孔径分布但孔径较大,气体多以努森扩散传递而导致分离性能偏低;在联合两者优点并取得突破后,将促进分子筛分机制膜的飞跃发展。
② 有机聚合物膜易于工业化生产,但相对无机膜而言,耐高温、机械性能仍待提高。通过对现有高分子膜材料进行改性或者制备高分子合金,成为新型气体分离膜开发的重要方向。
③ 混合基质膜兼具有机聚合物、无机材料的优点,但当前的膜产品多为两者随机掺杂;后续研究对相应排布进行可控调节,将显著提高膜性能。
注:本文内容呈现略有调整,若需可查看原文。